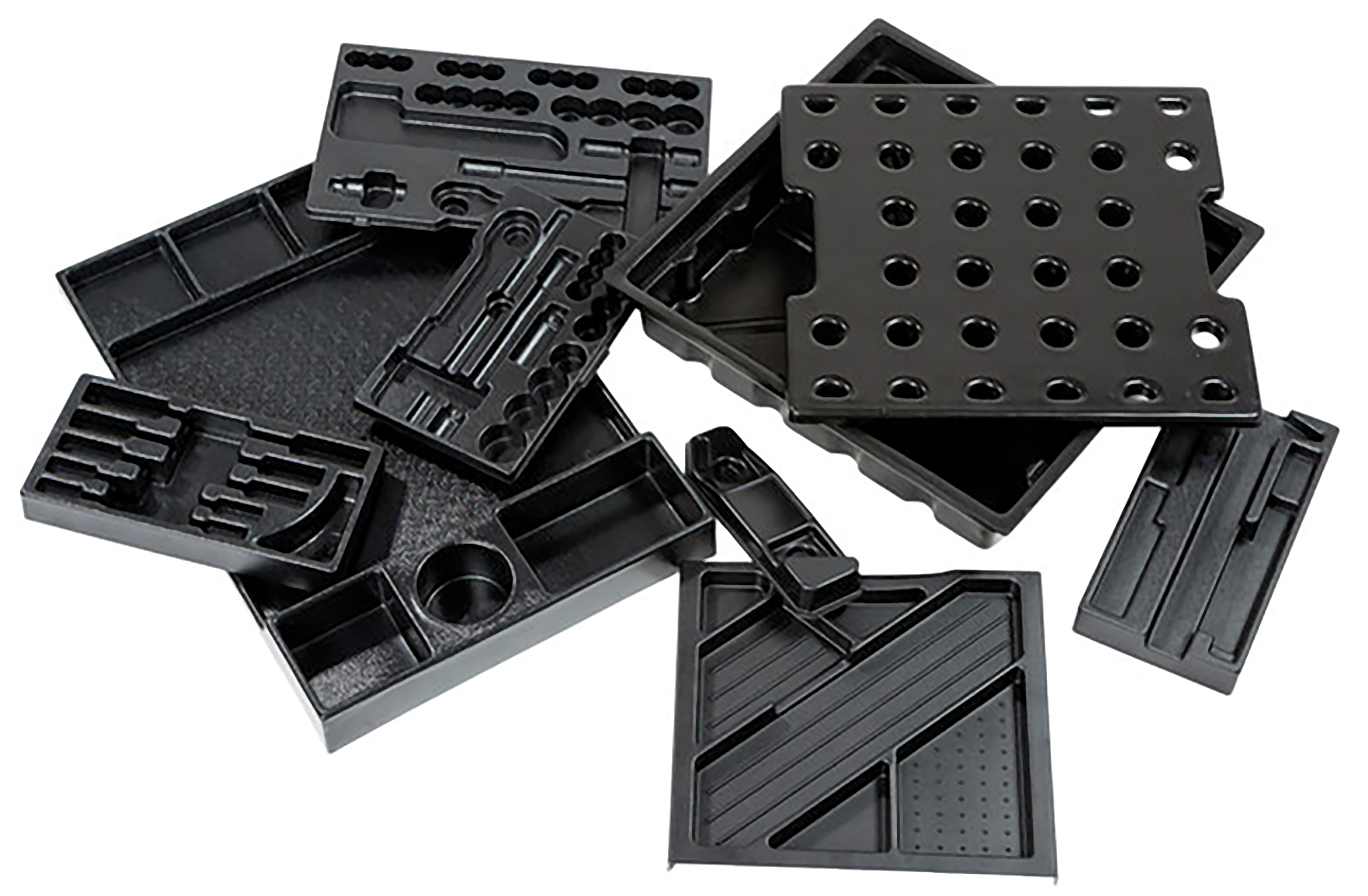
INTECH Thermoforming
Plastic sheeting being prepped for heating oven. The process of thermoforming begins by heating thin sheets of thermoplastic material until it becomes pliable and easy to manipulate. While still hot, the plastic is placed onto a rigid backing platform which is most often referred to as a mold. The material is secured by either vacuum pressure.

Thermoforming · Min Plastics & Supply, Inc.
Plastic Thermoforming is a plastic manufacturing process that applies a force (vacuum or pressure) to stretch a sheet of heated thermoplastic material (thermo) over an engineered mold to create a 3-dimensional shape or part (forming).

Cut Sheet Thermoforming Uses Which Type of Clamping System
Vacuum forming, a low-cost thermoforming process, offers an economical method of creating large-size, low-volume plastic parts. As a custom thermoforming specialist, Universal Plastics has all the answers to your vacuum forming questions. Read through the most frequently asked questions below, or call us at 800-553-0120 for more information.
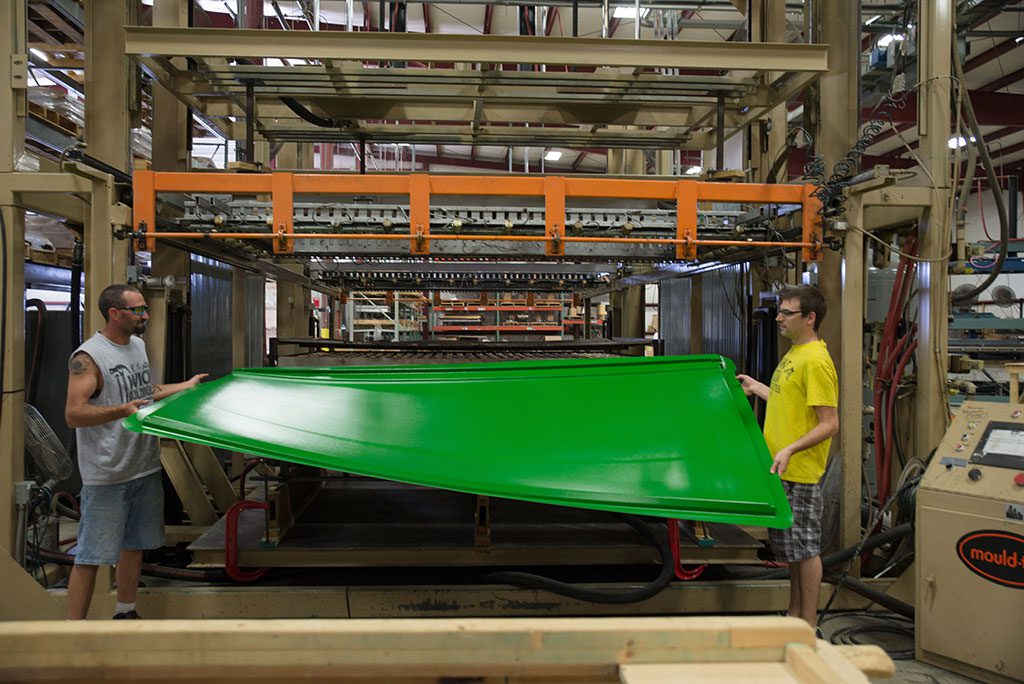
Thermoforming Products Plastics Unlimited
Some of the most common are: Introduction Vacuum Forming: This is the most basic process. In vacuum forming, vacuum alone is used to mold the part. The forming "pressure" is thereby limited to atmospheric pressure, about 14.7 psi. Pressure Forming: In pressure forming a pressure box is used on the side of the part opposite the mold.

Thermoformed Products Lyle Industries
The process is accomplished by applying heat and pressure (positive or negative) to stretch and conform a two dimensional thermoplastic sheet material onto temperature controlled molds to create custom three dimensional shaped structures and parts. PRIMARY FORMING TECHNIQUES

Accelerating Growth with Thermoforming Equipment SupplyOne
Step 1 is to heat the plastic sheet to a pliable temperature, then shape it to the mold using vacuum pressure, air pressure or a combination of both. Once the material has formed to the mold, it's cooled and removed from the mold, keeping its final shape. Since the final project cools against the mold surface under ambient temperatures.

Understanding Thermoforming Plastics Resources Inc.
PETG Plastic PETG, or polyethylene terephthalate - glycol modified has good clarity, impact strength, and moderate resistance to acids and alkalis. PETG is relatively easy to thermoform and can be heat or RF (radio frequency) sealed without getting cloudy.

Thermoforming in plastics processing Greiner Packaging
1) ABS. ABS is a common thermoformed plastic that is made of acrylonitrile, butadiene, and styrene. It can withstand extreme temperatures ranging from -4 to 176 °F. This ensures that the plastic can be molded to any desired shape at high temperatures. ABS is corrosion resistant and impact proof. This makes it an ideal polymer for 3D printing.

Which Plastic Materials Are Used In Thermoforming?
The process of thermoforming. In the thermoforming process, a thermoplastic sheet is heated to a temperature where it is pliable. It is, then, stretched over a mould and held in place while it cools and solidifies into the desired shape. The thermoplastic sheet is clamped and heated by an oven using either convection or heat until it is melted.
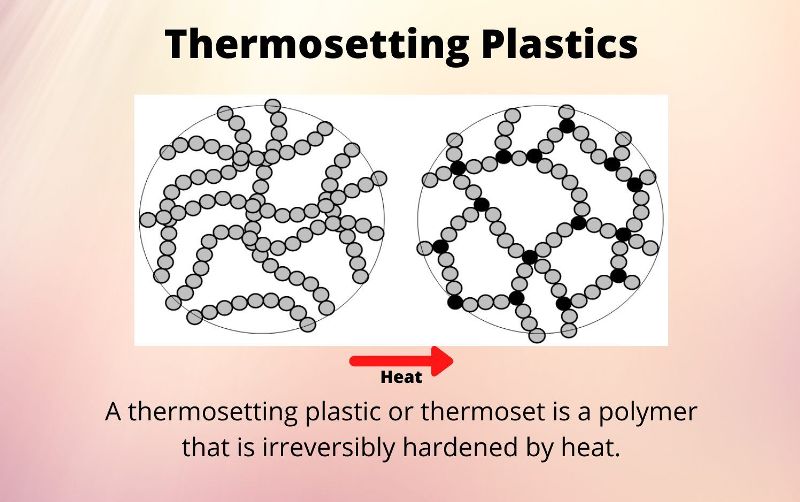
13 Thermosetting Plastic Examples in Daily Life StudiousGuy
First, a plastic sheet is heated to a temperature at which it becomes pliable. Then, the malleable plastic is cooled so it can harden into the desired shape. Types of thermoforming Pressure forming and vacuum forming are the most common thermoforming techniques.

a row of plastic stadium seats
Examples: ABS, HIPS, Polycarbonate Semi-crystalline thermoplastics Difficult to thermoform Examples: HDPE, PP Thermoplastic Triangle HDPE Semicrystalline, difficult to thermoform

Ways Your Everyday Life Would Be Harder Without Bronze Bushings National Bronze Manufacturing
The process of evacuating air from the sealed space between the hot sheet and the mold, thus allowing atmospheric pressure (14.7 p.s.i.) to force the sheet to conform with the contour of the mold. Applications: Non-critical appearance covers, dunnage trays, internal covers. Competes with sheet metal and fiberglass. A low- to medium-volume process.

Solution to problems associated with PET Thermoform plastic Packaging South Asia
Guides 15 minutes read Table of Contents What is Thermoforming? Plastic comes in different sizes, types, colors, and with different material characteristics. The wide variety of plastic makes it a crucial material for manufacturers interested in producing both prototypes and end-use parts for use.
Thermoforming Plastics and Thermosetting Plastics GCSE Design and Technology AQA Revision
Thermoforming is a manufacturing process where a plastic sheet is heated to a pliable forming temperature, formed to a specific shape in a mold, and trimmed to create a usable product. A plastic sheet is heated in an oven then stretched into or onto a mold and cooled to a finished form.

Thermoforming · Min Plastics & Supply, Inc.
. Thermoforming polymers Thermoforming polymers can be heated and formed repeatedly. They are pliable and recyclable . Acrylic sheet being laser cut PVC window frames 1 of 2 Slide 1 of 2, A.

Thermoforming Process Ultimate Guide 2019 With Cost Examples
A thermoforming primer. First, some basics: The process takes the form of either vacuum or pressure forming. In the former, a heated, pliable plastic sheet is pulled against the contours of the mold by vacuum pressure. "Since pressure is only applied to one side of the sheet," explains Formed Plastics Inc., "vacuum forming is typically.